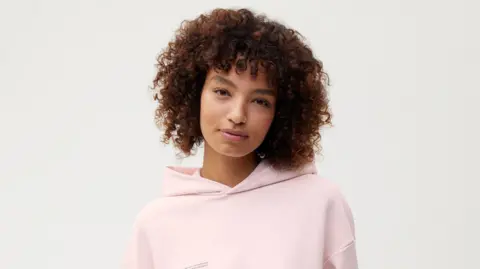
The price of clothing is more than the pound sign written on the tag, with fashion blamed for a significant chunk of the world’s carbon emissions and waste products.
But businesses and charities across the East of England are encouraging people to look at solutions during Sustainable Fashion Week – whether it’s a school uniform that can be completely recycled, toxic-free dyes, or the power of repair.
Colouring clothes with clever science
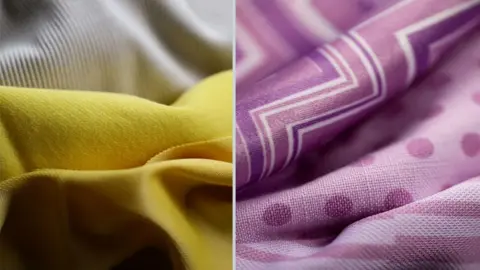
A team of Cambridge scientists include H&M and Pangaia in their clients after coming up with an ingenious way of dyeing fabric that doesn’t rely on toxic chemicals.
Colorifix, which now has its headquarters in Norwich, bioengineers microbes to produce different colours and then fix it to the cloth.
CEO Orr Yarkoni explained: “We find colours in nature, and instead of extracting the pigment, we borrow the information of how it’s made – we get hold of the code.
“That code is inserted into the microbes, which are fed sugar and nitrogen and convert them into pigment or dye.”
He said the process reduces water, electricity, pollution and carbon emissions compared to conventional dyes, which have a “heavy impact”.
“You’re taking a host of chemicals and heating it into a toxic soup. A lot of the chemicals used are also irretrievable – so once in the water system, you can’t get them out,” said Mr Yarkoni.
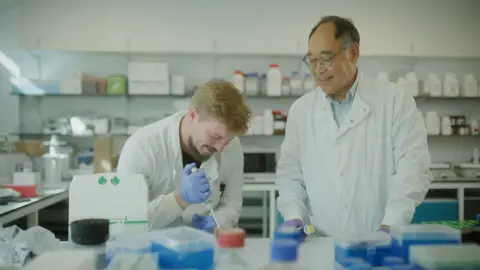
He was inspired to find an alternative method after seeing toxic waste in the rivers of Kathmandu and co-founded Colorifix with James Ajioka and David Nugent in 2016.
The company supplies coloured fabric to mills in Italy, Portugal, Brazil and India that supply clothing brands. Mr Yarkoni hopes they will be able to match or even beat the price of conventional dyes in future, as they “scale up” production.
“Not that we are working everywhere, but the technology is,” he explained.
He said their system could help existing factories to “move away from chemistry to biology”.
“We hope to show brands and manufacturers they can do the same thing without displacing everyone: you don’t need new dye machines or quality controls. You don’t need to start from scratch.
“To be sustainable, it has to be socially and financially sustainable; you don’t want to take jobs away or people’s livelihoods away,” he added.
Blazing a trail with school uniform
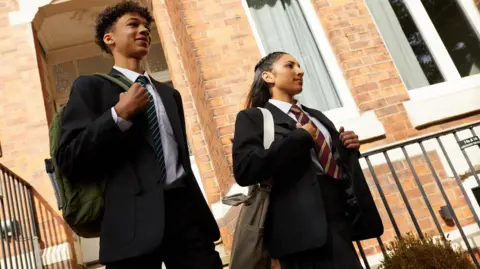
One golden rule of sustainable fashion is to make sure clothes are actually worn, used, and passed on instead of hanging unworn in wardrobes or – worse still – being thrown away in good condition.
So what about when an item is too damaged to wear?
At the moment, many clothes are incinerated, but what if you could turn the old garment back into yarn and remake a new version?
That is what Project Re:claim is hoping to do with school uniform blazers made by the company David Luke. A polyester recycling plant in Kettering run by the Salvation Army is already turning used textiles into new polyester yarn, in partnership with Project Plan B.
David Luke’s latest blazer has been redesigned so that it can be 100% recycled at that plant once it has been worn out, in a process known as the “circular economy”.
Every detail had to be rethought, from the lining to buttons and zips to adhesives.
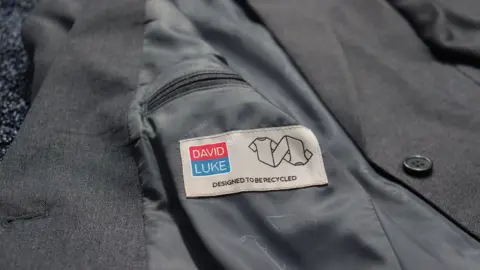
CEO of Project Plan B and the Circular Textiles Foundation Tim Cross said: “We now have the technology to enable David Luke’s blazers to be recycled without any separation of the garment, making it an efficient recycling process.”
In fact, the blazer is considered to be so ground-breaking that one has gone on display at the Design Museum in London, alongside works by fashion designers Stella McCartney and Priya Ahluwalia.
It is being showcased as part of “Tomorrow’s Wardrobe”.
Majonne Frost, head of environment and sustainability for Salvation Army Trading Company, said: “Our vision is to enable companies to produce uniforms, corporate wear, fashion garments and textile ranges using recycled polyester.
“This is an opportunity for companies to make a commitment to significantly reduce their environmental impact, and David Luke are showing us how that is possible.”
‘Stilettos to sneakers – we repair everything’
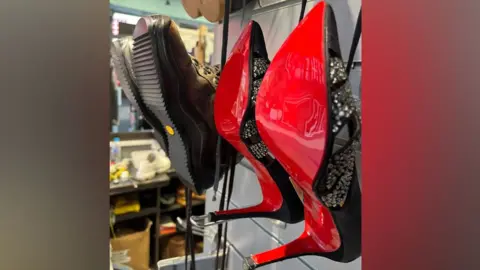
Keeping shoes on the pavement and out of the bin is the job of Andy Smith, who set up Shoesmiths in St Albans at the age of 21.
“All sorts of shoes can be repaired and many people don’t know that,” said Mr Smith, who has “moved with the times” to keep up with different trends in footwear.
“When stilettos were in fashion, I was so busy it was unreal,” he said.
“Youngsters are starting to come back again to get their trainers mended. Keen runners are doing a lot of miles and the shoes wear out – they’re expensive to replace, so getting them repaired is a better option.
“It’s a win for your wallet and for the planet”.
More than two million shoes are thrown away into landfill every week, according to charity Shoe Aid, so giving them a new lease of life can make a big difference.
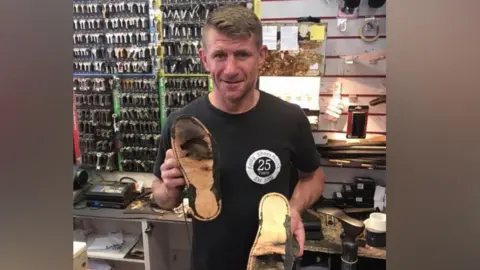
Mr Smith said the busiest period was about 20 years ago, when stilettos were in fashion.
“Everyone came in with them – stilettos wear out quickly. I’d have members of staff like a chain: one person would take the heel off, scour it down, pass it over to be glued up, and the next person would stick it on.”
He said they even fix shoes with moulded soles, but had this tip for anyone looking for footwear that is easy to mend.
“Good quality leather sole and separate heel are best. Rubber is normally OK; plastic is a bit of a pain, but we manage it.”
He admitted that shoe repair is seen as “a kind of old-fashioned thing”, but said younger people “are starting to recognise it as an eco-friendly option”.